The acceleration of electronic commerce has demanded new spaces to streamline the distribution of products and supplies in cities. In this sense, the logistics and real estate sectors occupy a relevant position.
For the customer, free shipping is a very attractive option when buying a product. In Mexico, 43% of businesses do not charge, and this directly benefits businesses, since it generates positive expectations among buyers (1).
In addition, the concentration of volume in the distribution centers is key, since the more volume, several distribution points are occupied, the distances for delivery are shortened and the cost of transporting the product is reduced (1).
Industrial sectors focused on logistics have registered up to 40% growth, compared to 23% in 2019 (2).
▬
Other indicators that allow evaluating the logistics performance of businesses are: customs permits for international shipments, infrastructure, tracking and tracing information offered to the customer, as well as delivery timeliness, according to the World Bank (1).
In this sense, distribution centers (CEDIS) are real estate products of great support to optimize the entry and exit routes of products at strategic points in the city.
If you are interested in knowing more about industrial zones, we suggest you read:
“Industrial areas for rent in Mexico City: concepts, locations and trends.”
What is a distribution center?
It is defined as a logistics space where merchandise is stored and incoming and outgoing orders are dispatched for the distribution of articles to the wholesale or retail trade (3).
Distribution centers consist of one or more warehouses , where the merchandise is disposed and treated according to your requirements, for example, in freezing areas. There is also a special area to prepare orders (3).
In the CEDIS, delivery orders are listed according to the times established between the supplier and the customer (3).
▬
Main objectives of the distribution centers (CEDIS) are: store, control, guard and dispatch, efficiently, inventories, Therefore, it is very important to keep a control on the storage of the merchandise, with the lowest possible operating cost (3).
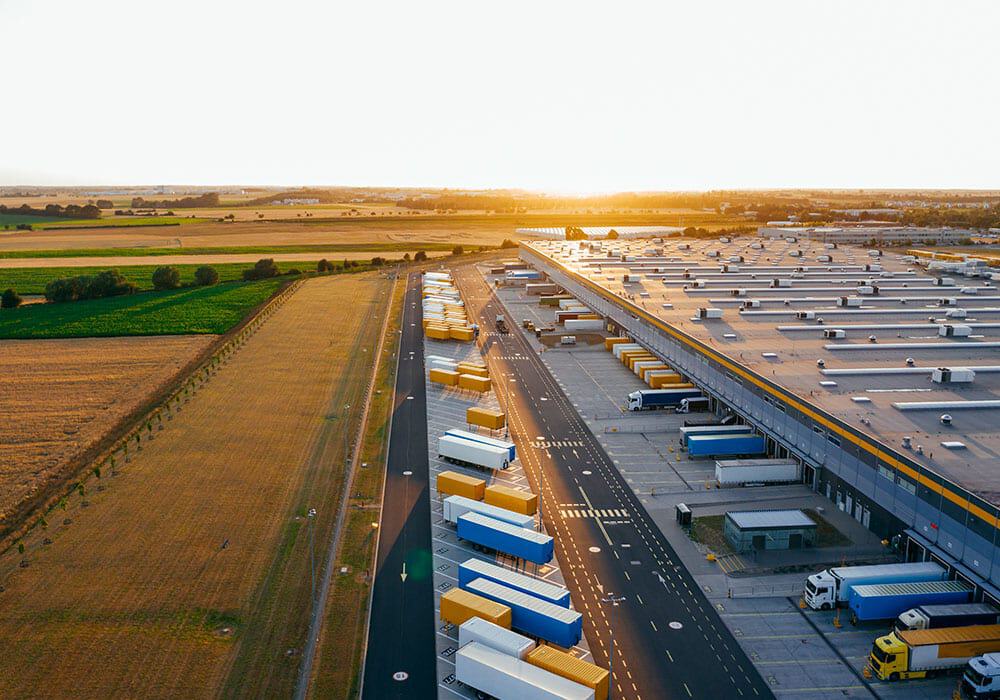
Types of CEDIS
The types of CEDIS or department stores depend on five classifications, according to (4):
• Your role in the logistics network:
1. Consolidation. A series of orders from different suppliers are grouped together to make a larger volume delivery to the same customer, in order to reduce transportation costs.
2. Splitting of shipments or break-up. Here it is the other way around: if a large order arrives, it is broken down into small deliveries that are provided to the end customer.
• Their geographical location and the activity they carry out:
Central. Supplies from the production centers arrive at this CEDI and from there they go to the regional distribution points.
Regional. From this center it is distributed to the points of consumption, so the unloading and loading of goods is constant and ideally should be processed in less than a day.
3. Transit. In this type, mobility is very effective, since it is an intermediate point that covers more reception and dispatch areas.
• Tax treatment of stored products:
1. General. This refers to products that do not enjoy tax exemptions, and therefore the discounts in force apply.
2. Special. In this case, the goods are exempt from taxes while they are in that space, such as free trade and customs zones.
• The warehouse area:
1. Open. Center with products in the open air, whose conditions do not need to be delimited or cared for under a roof.
2. Covered. This type of CEDI is the most common, since it requires a building or warehouse to protect the goods.
• The degree of automation:
Conventional. This type of center consists of racks and aisles with adequate sizes for the transfer of goods.
2. Automated. This large warehouse is occupied and energized with automated equipment and machinery for the transfer and disposition of products.
This diversity of objectives it depends on the requirements that distribution centers meet for your business , in its different commercial and industrial stages. At Vallejo Properties we are attentive to your expansion plans. Consider the warehouse rental for CEDIS and contact us for more details.
If you want to know more about wineries for rent, consult :
“Warehouses for rent in CDMX: characteristics and recommendations.”
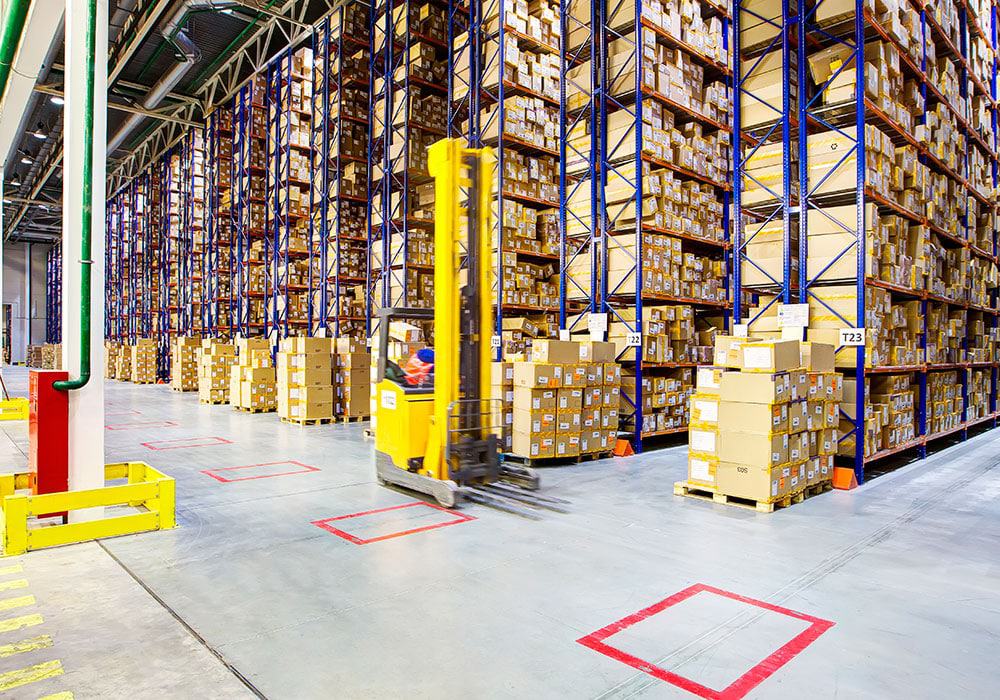
Examples of distribution centers in Mexico
The opening of CEDIS is a common practice , especially for companies with transnational objectives, as they need to constantly move their products and make them reach consumers and other distributors.
So far in 2020, CEDIS have been opened for companies such as:
– Merck. Pharmaceutical focused on science, technology and chemistry, with more than 350 years of experience, located in 66 countries and with more than 55 thousand employees. Its expansion is done with the purpose of expanding its warehouse of life sciences, in the State of Mexico (5).
– Walmart. This large supplier inaugurated a CEDI in the State of Mexico to strengthen its omnichannel logistics, according to the demand in its
ecommerce platform
. His investment was 600 million pesos. In addition, the company plans to open two other centers in Yucatán and Chihuahua (6).
– Logisfashion. This logistics outsourcing company in the fashion, lifestyle and ecommerce sector, opened its third distribution center (in the country) in the State of Mexico with 12 thousand square meters of operational area (7).
– Mercado Libre. The largest marketplace in Latin America will invest 27.1 million dollars for its third CEDI in the country. It will be built to meet the demand in the Bajío area, in the state of Jalisco, and will have an area of 60 thousand square meters, with the idea of expanding it to 80 thousand (8).
As you see, the State of Mexico is an important investment area for the profiles of large competitors. In fact, this entity generates 10.1% of Mexico’s manufacturing outputIt remains a leader, mainly in the paper industry, furniture, as well as petroleum and coal products (9).
This has as a precedent the installed capacity that the state has reached in its production rhythm, with a great impact on the export issue, as a result of the widespread investment in the Metropolitan Area, which represents, among other things, a conformation of industries and strategic complexes coming from the country’s capital city. (10).
At Vallejo Properties we have warehouses that can adapt to your distribution requirements in Tultitlán, a highly relevant industrial estate in the State of Mexico. Contact us to share more details.
If you are looking to know the current trends in wineries, check our article:
“Wineries: trends, projections and recommendations for the sector after the pandemic”.
What characteristics should distribution centers have?
It is essential that they have, physically, ramps, pallets, pallets , safe accesses, refrigerators, if it is the case, among other infrastructure specifications that are required for the entry, conservation and exit of the merchandise.
It is important to consider that the products should remain as short as possible and be moved minimally inside the center (3).
▬
The important thing about CEDIS is to be a key point in the distribution route of the goods, with proximity to the main routes of mobility in the city, since the location is an important strategic factor.
Other additional elements that distribution centers can count on are: forklifts, baskets, shelves, forklifts, conveyor belts, applicators and stevedores, especially for the handling and mobility of materials, since facilitate set-up time and minimize product damage (3).
It is also necessary to have areas where other tasks are carried out, such as reception, inspection, storage (of goods, machines or systems), clearance and customs (3).
Equally important are spaces complementary, such as offices, workshops, dressing rooms, returns area, infirmary, dining rooms , battery area, garbage and waste classification, among others (3).
In other words, it is not only a large space for the operation of goods, such as a warehouse. warehouseThe distribution center also involves considering areas for administrative tasks related to the mobility of goods.
In the CEDIS it is very important to separate each area to avoid episodes of contamination or accidents, so the staff must be clear about where and how to carry out each activity.
▬
In this sense, the design of the place is fundamental from its construction or even in the adaptation of a space, such as a winery. At Vallejo Properties we have properties that can respond to your distribution projects, with excellent locations in Mexico City and the State of Mexico. Write to us and let’s work in your ideal space.
With the issue of springs there must be several, especially if you plan to expand. We recommend optimizing space by placing the storage and shelving areas parallel to the longest axis of the warehouse (3). In addition, the number of docks must be proportional to the square meters of the place.
On the other hand, the central office of the chief or area chief must be high to control the entire operation and have visibility of the activities (3). Finally, it is suggested that the merchandise is ordered alphabetically to reduce search and travel times inside the property (3).
What is the difference between a warehouse and a CEDI?
The warehouse is part of a distribution center, since it allows the protection of merchandise by sections, according to the storage criteria (time, type of product and treatment) (3).
In this sense, CEDIS are specialized facilities, with patios, wings with loading and unloading positions, pneumatic ramps, curtains by position, among other elements.
As we saw, the CEDIS also cover administrative areas. Further, handle high demand products (4) , so mobility is constant, Unlike a warehouse that can keep items for longer because its objective is to protect, and not necessarily to mobilize.
If you are interested in industrial warehouses, because of your business, we suggest you review:
“Industrial warehouses: characteristics, areas and recommendations”.
How are distribution centers managed in Mexico?
At first, It is essential to have a record of the materials that are stored: packaging, semi-finished, raw materials.
Likewise, it is necessary to have structures, tools and equipment that allow to mobilize the entry and exit of products and supplies from the trucks that enter or transfer (3).
This makes the mobility of goods more efficient and reduces physical risk to operating personnel (3). In addition to inventory registration, it is very important have a staff control for accesses, activities, equipment used and spaces designated for tasks.
It is also important to be clear about the points of the general process carried out within a CEDI (3) (11):
1. Picking. This first stage depends on the movement of orders and vehicle dispatch. All picking must be done based on ergonomics, routes, productivity, space, technology, and infrastructure.
2. Storage / Inventory. In this phase the product is classified according to the criteria established for it. This categorization profile must be made based on the volumetric needs of the supply and marketing policies, considering density, storage peaks and operating vacuum.
3. Reception. Goods are entered, verified and recorded, according to storage positions or dispatch locations, in addition to considering movements, storage time and the types of docks required.
4. Projections. It is important to consider that in distribution centers there are different temporalities within the operation, so peaks must be contemplated to avoid interruptions or major impacts within the planning of storage, receipt, dispatch and collection.
5. Additional areas. It is useful to have control and management of the aspects around the center: the land, parks, offices, green areas, as well as the physical and legal limits for a possible expansion or creation of a different layout .
In addition to this, the administrative area of the center should be considered: bathrooms, dressing rooms, lockers, meeting rooms, training areas, dining rooms, pump room, power plants and networks, maneuvering yards, among other elements.
With these clear points, the management of the distribution center will flow in a better way, having control and care in each of the operational and administrative phases.
If you want to know more about the real estate companies in the area, see:
“Real estate in CDMX: trend guide, companies and recommendations after the pandemic”.
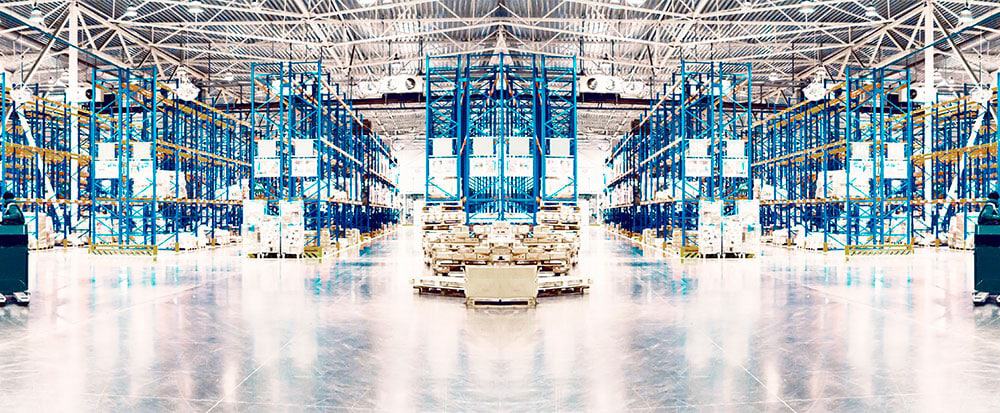
Technological and logistical trends of the CEDIS
The distribution centers are based on WMS (Warehouse Management System), which is a online execution system, whose objectives are based on controlling the records of personnel, inventories, equipment and spaces (3).
This tool is valid for order preparation, employee management, inventory classification and control, units of measure, the establishment of rules for storage and distribution, as well as the receipt and location of materials, according to with the expiration and manufacturing dates, as well as the serial and batch number (3).
In addition to this tool, there are other very important and current elements in the logistics sector (12) (13):
– Technological advances on the road to “intelligence”. The world does not stop, much less now that digital is growing at a very fast speed. The fields in robotics, artificial intelligence, Big Data, el SEOespecializado para este sector and visibility in the supply chain is summarized in the integration of all these components in a digital and optimized way, with technologies such as vision or the voice picking (augmented reality in order picking), which are under development.
– Green logistics. The issue of impact at high levels is being considered in a relevant way to run logistics chains more efficiently, through the use of sustainable means of transport and the use of less polluting packaging materials.
– Exoskeletons. This technological aspect stands out because it focuses on the creation and optimization of robots that move goods, notably reducing the risk of significant physical damage to personnel, and being executed with greater speed and effectiveness.
– Digitization of the supply chain. Greater transparency regarding transit (especially in the last mile). the last mile) and delivery of materials and products, with the idea of keeping the consumer informed of their status at all times. This includes data management, as well as the reliability and security of the data.
– Automation. This includes projected damage, such as expiration, lost products, slow processes, returns, and productivity issues. The expectation is to generate more responsive and proactive conversions, through data management and scenario projection.
The current trend is to synchronize the digital and the physical in the logistics industry based on distribution centers.
▬
In this sense, the generalized situation of the stay at home economy (2), whose current economy demands that most of the population be at home, working and shopping remotely.
This point is essential because the spaces that currently house merchandise require larger dimensions, since online inventories are up to three times more in demand (2).
In this sense, the demand for ecommerce coverage is greater, so new spaces must be considered. dedicated to respond to these situations in places where CEDIS are present, and even where they are not, to cover more ground and competition from new business models and strategic alliances.
Remember that in Vallejo Properties You can count on us to find and adapt the ideal space for the present of your business, with a future perspective. Write us and know the location of the distribution centers in our catalog.
If you want to know more about the real estate market, we recommend you read:
“ Real estate market: spaces, trends and projections 2020-2021 “
References
1. Marisol Morelos.
Shipping logistics will be key in the growth of e-commerce in Mexico.
. The CEO, 2020. Retrieved September 8, 2020.
2. Adriana Holohlavsky.
Warehousing: trends in Mexico and Latam.
.
Inbound Logistics Latam, 2020. Retrieved September 9, 2020.
Logistics Zone. What is a distribution center? Logistics Zone, 2018. Retrieved September 7, 2020.
4. Noega Systems.
Types of warehouses in the logistics chain and their characteristics.
.
Noega Systems, 2016. Retrieved September 8, 2020.
5. T21.
Miebach designs expansion of Merck Cedis
.
T21, 2020. Retrieved September 7, 2020.
6. T21.
Walmart inaugurates a new store in the State of Mexico.
.
T21, 2020. Retrieved September 7, 2020.
7. T21.
Logisfashion opens a new cDi’s in Mexico; changes general manager.
.
T21, 2020. Retrieved September 7, 2020.
8. Enrique Duarte.
Mercado Libre announces investment in a new cis in Jalisco.
.
T21, 2020. Retrieved September 7, 2020.
9. Alondra Avila. Edomex produces 10.1% of the country’s manufacturing: Sedeco. Millennium, 2019. Retrieved September 17, 2020.
10. Gonzalo Castañeda. Report on the economic complexity of the State of Mexico. Center for Economic Research and Teaching (CIDE) and Ministry of Finance and Public Credit (SHCP), 2017. Retrieved September 17, 2020.
11. Logistics Magazine.
Ten key elements in the logistics design of a CEDI.
.
Logistics Magazine, 2016. Retrieved September 8, 2020.
12. Juan Luis de los Ríos Sánchez.
The 2020 logistics trends that will take you the furthest.
.
IEB School, 2019. Retrieved September 8, 2020.
13. Manuel Nieblas.
Industry 4.0 and Distribution Centers.
.
Deloitte, 2016. Retrieved September 9, 2020.